Graphite Flotation
Flotation is a commonly used and important mineral processing method. With good natural floatability, basically all forms of graphite can be purified by flotation. In order to protect the flakes of graphite, the multi-stage process flotation is mostly adopted. Generally, the kerosene is used as collector, with a dosage of 100-200g/t, and the terpenic oil or butyl ether oil is used as frother, with a dosage of 50-250g/t.
Because graphite has good natural floatability, the flotation method can increase the grade of graphite to 80% to 90%, or even up to about 95%. The biggest advantage of this method is that it has the lowest energy and reagent consumption and the lowest cost among all purification solutions.
The extremely fine silicate minerals mixed in the graphite flakes and compounds of potassium, calcium, sodium, magnesium, aluminum and other elements cannot be dissociated by grinding, and it is not conducive to protecting the large graphite flakes. Therefore, flotation is only a primary method for purifying graphite. To obtain high-carbon graphite with a carbon content of more than 99%, it must be purified by other methods.
1. Flotation process
Flotation process: The flotation method is mainly based on the surface wettability difference between graphite and gangue mineral. Since graphite has good hydrophobicity, it will adhere to and float up with the bubbles, while hydrophilic gangue will remain in the water, thereby achieving flotation separation.
The flotation process mainly includes three parts: ore preparation and crushing, grinding, and slurry mixing and flotation.
(1)Ore preparation and crushing
Crushing process: It often uses three-stage opening, two-stage opening or one-stage opening process. If it is a small mine of weathered ore, the ore can be ground directly without crushing. Jaw crushers are often used for coarse crushing of large-grained minerals; hammer crushers and impact crushers are used for secondary crushing of minerals, and cone crushers and roller crushers are used for fine crushing of minerals.
(2)Grinding
Grinding: The grinding stage is to further realize the dissociation of graphite monomers or locked particles after crushing. In order to select large flake graphite early, the multi-stage grinding process is often used, combined with flotation to complete the separation. At this stage, ball mills, rod mills, and stirring mills are commonly used as grinding equipment.
Classification: Classification equipment and grinding equipment form a grinding and classification operation, which separates solid particles according to their size in order to timely get products with qualified particle size. Hydrocyclones and spiral classifiers are commonly used as classification equipment for graphite classification.
(3)Slurry mixing and flotation
Slurry mixing: It is an important process in the mineral purification and separating process, which can prepare for subsequent separating operations. Generally, the agent is dispersed and fully contacted with the graphite mineral by the adjustment of the slurry concentration.
Flotation: The flotation process is different according to the type of graphite. The conventional flotation process is generally a closed-circuit process of multi-stage and sequential or centralized return of medium ore. When each stage of grinding operation is completed, it enters the flotation stage. For example, after the first stage of grinding (about 40% ore particles are -200 mesh), a stage of flotation is performed, followed by multi-stage grinding and multiple separations; The return of medium ore is a process in which the medium ore after flotation is returned to the previous level of operation in sequence or concentratedly to improve the efficiency of graphite ore flotation. In the specific plan, we will design different return processes according to customer needs, such as concentrated return or sequential return.
2、Flotation agent
(1)Collector
Graphite itself has a certain degree of floatability. Graphite concentrate can be flotated without using a collector, but the efficiency is not satisfactory. Therefore, a collector can be added appropriately to form a layer on the surface of the graphite ore. The thin oil film enhances the hydrophobicity of the graphite and allows it to adhere firmly to the bubbles, thereby improving the floatability of graphite and the recovery rate of concentrate. Common collectors for graphite ore mainly include: kerosene, diesel, liquid paraffin, heavy oil and other hydrocarbon oil, etc.
(2)Frother
Frother is composed of the polar molecule and non-polar molecule. The former is hydrophilic and the latter is hydrophobic. By adding a frother, the mechanical strength of the bubbles can be increased, and at the same time, the number, size and rising speed of the bubbles can be controlled, and the distribution of the bubbles can be changed. Commonly used frothers for graphite ore include 2# oil, 4# oil, pine oil, cresolic acid and camphor oil, etc.
(3)Regulator
The purpose of the regulator is to adjust the interaction between the collector and the mineral to inhibit or strengthen the hydrophobicity of the mineral. According to different functions, regulators can be divided into three types: pH modifier, depressant, and dispersant.
pH modifier: Lime (CaO), NaCO3, Na(OH)2 are commonly used;
Depressant: There are mainly water glass, sodium carboxymethyl cellulose, EDTA, tartaric acid, citric acid, oxalic acid, etc;
Dispersant: There are mainly water glass, sodium hexametaphosphate, sodium polyacrylate, etc.
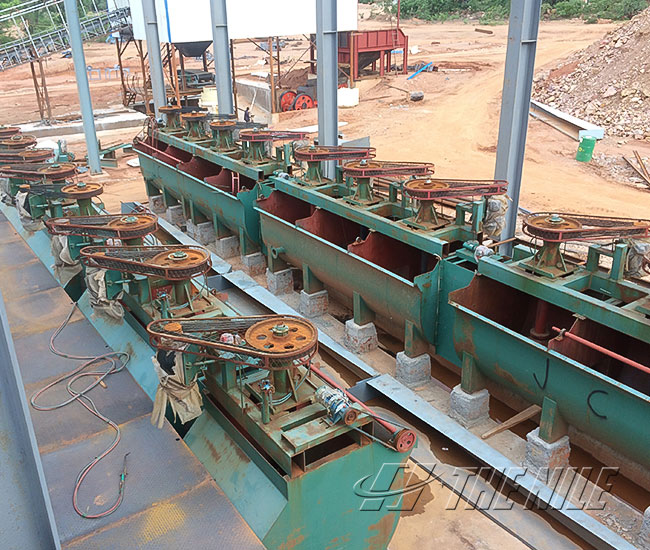
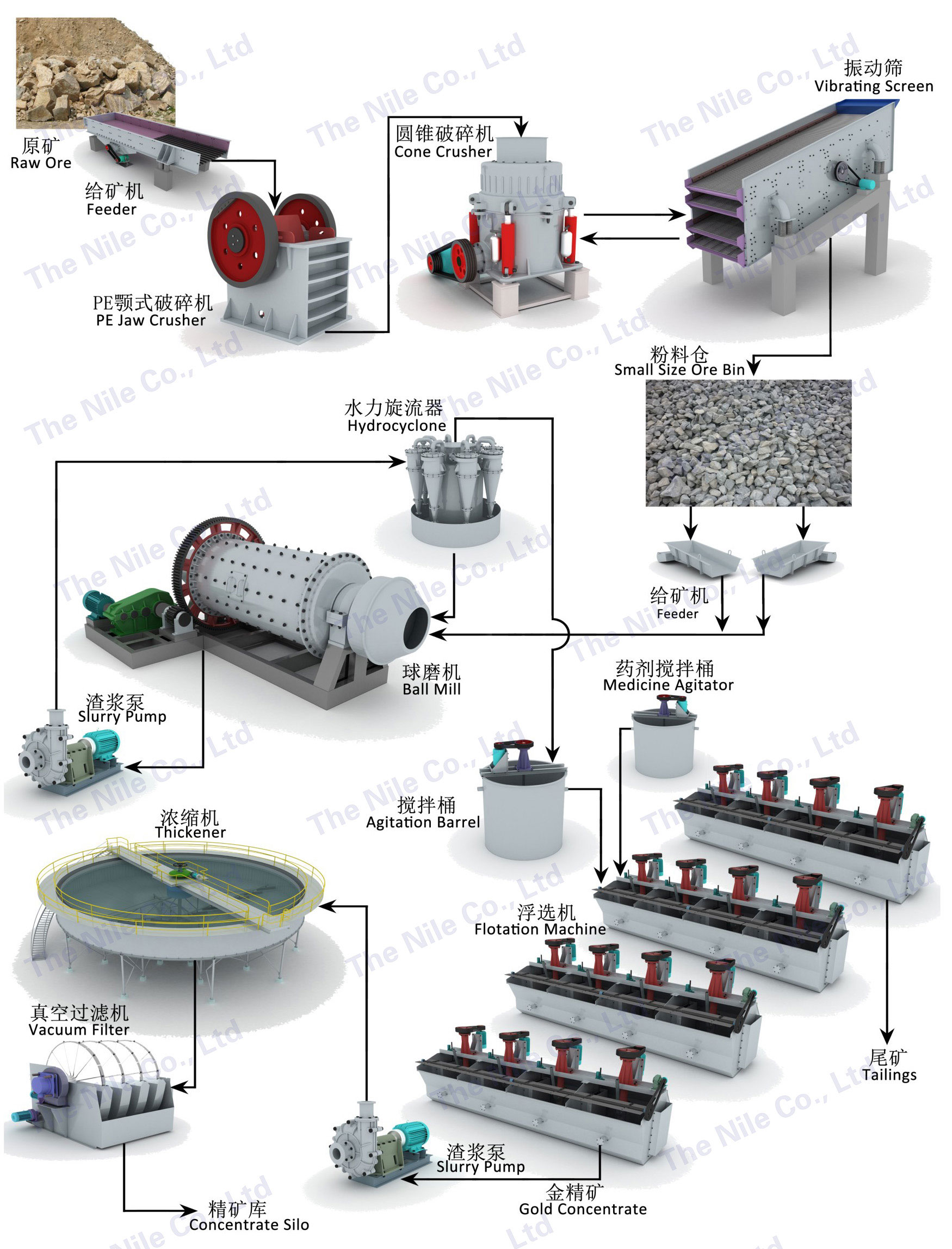
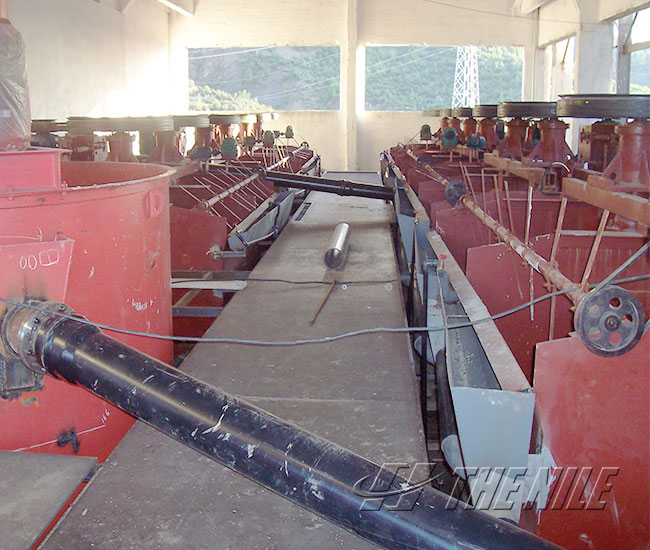
Flotation process: The flotation method is mainly based on the surface wettability difference between graphite and gangue mineral. Since graphite has good hydrophobicity, it will adhere to and float up with the bubbles, while hydrophilic gangue will remain in the water, thereby achieving flotation separation.
The flotation process mainly includes three parts: ore preparation and crushing, grinding, and slurry mixing and flotation.
(1)Ore preparation and crushing
Crushing process: It often uses three-stage opening, two-stage opening or one-stage opening process. If it is a small mine of weathered ore, the ore can be ground directly without crushing. Jaw crushers are often used for coarse crushing of large-grained minerals; hammer crushers and impact crushers are used for secondary crushing of minerals, and cone crushers and roller crushers are used for fine crushing of minerals.
(2)Grinding
Grinding: The grinding stage is to further realize the dissociation of graphite monomers or locked particles after crushing. In order to select large flake graphite early, the multi-stage grinding process is often used, combined with flotation to complete the separation. At this stage, ball mills, rod mills, and stirring mills are commonly used as grinding equipment.
Classification: Classification equipment and grinding equipment form a grinding and classification operation, which separates solid particles according to their size in order to timely get products with qualified particle size. Hydrocyclones and spiral classifiers are commonly used as classification equipment for graphite classification.
(3)Slurry mixing and flotation
Slurry mixing: It is an important process in the mineral purification and separating process, which can prepare for subsequent separating operations. Generally, the agent is dispersed and fully contacted with the graphite mineral by the adjustment of the slurry concentration.
Flotation: The flotation process is different according to the type of graphite. The conventional flotation process is generally a closed-circuit process of multi-stage and sequential or centralized return of medium ore. When each stage of grinding operation is completed, it enters the flotation stage. For example, after the first stage of grinding (about 40% ore particles are -200 mesh), a stage of flotation is performed, followed by multi-stage grinding and multiple separations; The return of medium ore is a process in which the medium ore after flotation is returned to the previous level of operation in sequence or concentratedly to improve the efficiency of graphite ore flotation. In the specific plan, we will design different return processes according to customer needs, such as concentrated return or sequential return.
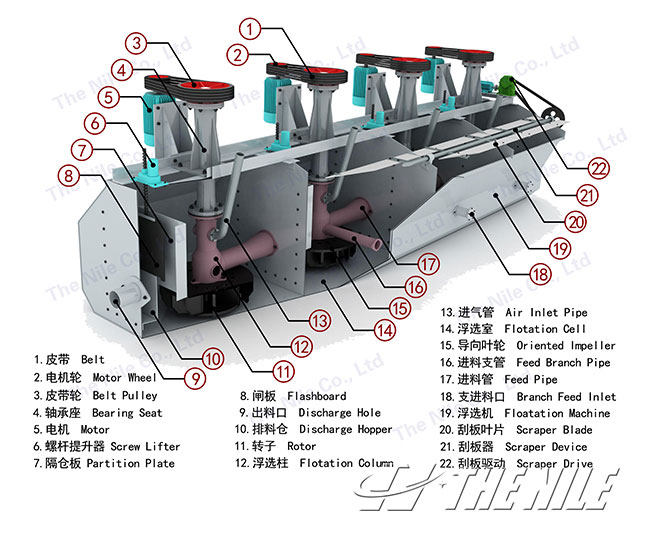
2、Flotation agent
(1)Collector
Graphite itself has a certain degree of floatability. Graphite concentrate can be flotated without using a collector, but the efficiency is not satisfactory. Therefore, a collector can be added appropriately to form a layer on the surface of the graphite ore. The thin oil film enhances the hydrophobicity of the graphite and allows it to adhere firmly to the bubbles, thereby improving the floatability of graphite and the recovery rate of concentrate. Common collectors for graphite ore mainly include: kerosene, diesel, liquid paraffin, heavy oil and other hydrocarbon oil, etc.
(2)Frother
Frother is composed of the polar molecule and non-polar molecule. The former is hydrophilic and the latter is hydrophobic. By adding a frother, the mechanical strength of the bubbles can be increased, and at the same time, the number, size and rising speed of the bubbles can be controlled, and the distribution of the bubbles can be changed. Commonly used frothers for graphite ore include 2# oil, 4# oil, pine oil, cresolic acid and camphor oil, etc.
(3)Regulator
The purpose of the regulator is to adjust the interaction between the collector and the mineral to inhibit or strengthen the hydrophobicity of the mineral. According to different functions, regulators can be divided into three types: pH modifier, depressant, and dispersant.
pH modifier: Lime (CaO), NaCO3, Na(OH)2 are commonly used;
Depressant: There are mainly water glass, sodium carboxymethyl cellulose, EDTA, tartaric acid, citric acid, oxalic acid, etc;
Dispersant: There are mainly water glass, sodium hexametaphosphate, sodium polyacrylate, etc.
Request for Quotation
You can get the price list and a NILE representative will contact you within one business day.