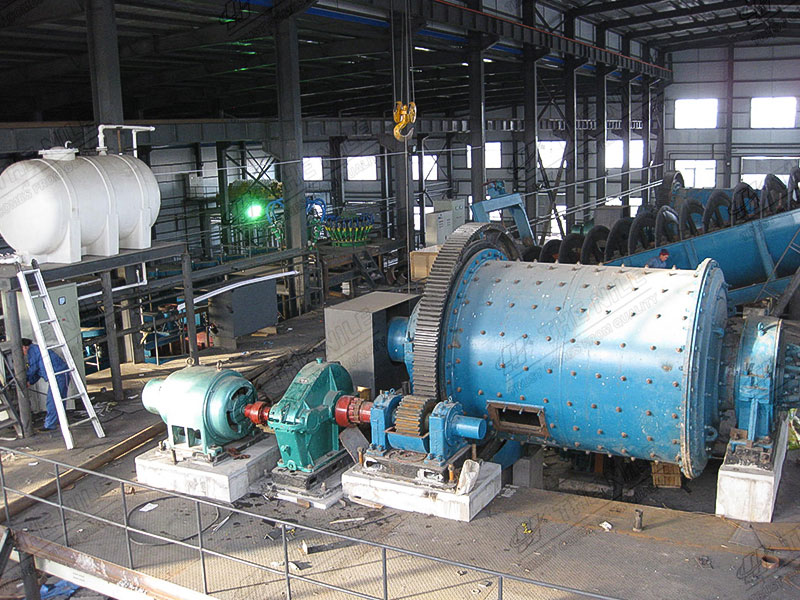
Fluorite ore beneficiation process
Common fluorspar beneficiation methods mainly include hand separation, gravity separation and flotation. In view of the dilution of fluorite raw ore and the fluorite and vein Due to the interlocking characteristics of stones, flotation has become the main beneficiation method currently used to separate fluorspar and gangue minerals.
Easy ways to get the answers you need. Service Online
Common fluorspar beneficiation methods mainly include hand separation, gravity separation and flotation. Among them, the hand separation method is often used as an auxiliary means for other fluorite beneficiation methods. The gravity separation method is suitable for the production of metallurgical grade lump ore or as a pre-selection operation for the fluorspar flotation process. In view of the dilution of fluorite raw ore and the fluorite and vein Due to the interlocking characteristics of stones, flotation has become the main beneficiation method currently used to separate fluorspar and gangue minerals.
Fluorite ore hand selection method
The hand separation method is mainly used in fluorspar ores where the boundaries between fluorite and gangue are very clear, waste rocks are easy to remove, and various grades of ores are easy to identify with the naked eye. It is the simplest and most economical mineral processing method. The fluorite hand selection method mainly includes washing, screening and hand selection operations. The raw ore after punching and screening can be divided into large pieces, medium pieces, and particles (particle size 6-15mm) and enter the manual selection field. They are manually selected according to grade and stacked by grade. The particle ore enters gravity separation and separation, and is crushed. The chips are processed into fluorspar concentrate through flotation.
Quartz-type fluorite ore:The main minerals are fluorite and quartz, and the fluorite content can reach 80% to 90%. Contains small amounts of calcite, barite and sulfide. Quartz-type fluorite ore is mainly composed of fluorite (content up to about 85%) and quartz, with only a small amount of calcite, barite and sulfide present. The key to sorting is mainly to reduce silicon in the concentrate. To separate quartz from fluorspar, quartz and fluorspar monomers must be dissociated through grinding, so grinding is an important factor affecting quartz-type fluorspar flotation. The most reasonable method is to adopt a staged grinding process, which can not only reduce the silicon content in the fluorspar concentrate after flotation, but also increase the recovery rate of the fluorspar concentrate.
Carbonate fluorite ore: the main minerals are fluorite and calcite. The calcite content can reach more than 30%, with a small amount of quartz, sometimes forming a quartz-calcite-fluorite type ore.
Barite type fluorite ore: the main minerals are barite and fluorite, and the barite content reaches 10% to 40%. This type of ore is often accompanied by sulfides such as pyrite, galena, sphalerite, etc. Sometimes the quartz content increases to form a quartz-barite-fluorite type ore. The flotation of barite-type fluorite ore generally first uses a mixed flotation process and Na2CO3 to adjust the pH value of the slurry, and use oleic acid and water glass as collectors and inhibitors respectively to obtain fluorite and barite. The concentrate is mixed and the barite and fluorite are separated by flotation.
Sulfide-type fluorite ore: Its mineral composition is basically the same as quartz-fluorite, but it contains more metal sulfides, and sometimes the lead and zinc content can reach industrial grades. For sulfide ore-type fluorspar ores, sulfide ore collectors can generally be used to select metal sulfide minerals first, and then fatty acid collectors can be used to recover fluorspar from flotation tailings. In addition, roasting, leaching and other processes can also be used to extract valuable metals and decompose fluorspar. The process flow is relatively simple and can produce high-quality fluorspar products while comprehensively recycling valuable metals.
Application of mineral processing equipment in fluorite ore
Case 1: 500 tons of raw ore are processed daily
Process: 500 tons of raw ore are processed daily. The crushing process is two-stage semi-closed circuit crushing. The crushing particle size is -15mm. The raw ore goes through two stages of closed-circuit grinding. -0.074mm accounts for 78%. The raw ore grade is 21%. After the first coarse, second sweep, and seventh The grade of fluorspar concentrate is 95%, and the recovery rate is 85%. The fluorspar undergoes two stages of dehydration, and the tailings undergo two stages of dehydration and are stacked in dry discharge.
Main equipment: 1 PE600 Jaw Crusher, 1 2YA2148 Vibrating Screen, 1 PEX300*1300 Fine Jaw Crusher, 1 4 1/4 Simons Cone Crusher; 1 MQG2430 Ball Mill, 1 FG- 20Ф2000 Spiral Classifier, 1 MQY2430 Ball Mill, 1 4*250 Cyclone Group, 12 XCF4 Flotation Machines, 22 KYF Flotation Machines; 1 Ф15m Thickener, 1 45㎡ Ceramic Filter, 1 Ф24m Thickener and 1 22㎡ Rubber Belt Filter.
Case 2: 500 tons of raw ore are processed daily
Process: 500 tons of raw ore are processed daily. The crushing process is two stages and one closed circuit. The damage particle size is -15mm. The raw ore is ground in two stages of closed circuit. -0.074mm accounts for 85%. The grade of raw ore fluorite is 40% and barite is 40%. The first Mixed flotation desliming, priority flotation of fluorite, using a semi-open circuit process, fluorite flotation through the first coarse and sixth fine, the concentrate grade is 97%, the recovery rate of fluorite concentrate is 80%; fluorite flotation tailings flotation To select barite, the barite goes through drug-free flotation before flotation, and then goes through primary roughness and secondary fineness. The concentrate grade is 90% and the concentrate recovery rate is 76%.
Main equipment: 1 PE500*750 Jaw Crusher, 1 GP100 Cone Crusher, 1 YA1236 Vibrating Screen, 1 MQG2430 Ball Mill, 1 FG-20Ф2000 Spiral Classifier, 1 MQY2136 Ball Mill, 1 4* 250 Cyclone Groups, 10 BF-8, 25 BF-4, 2 Ф16m Thickeners, 4 20㎡ Disc Type Filters, 2 Ф2*12 Dryers.
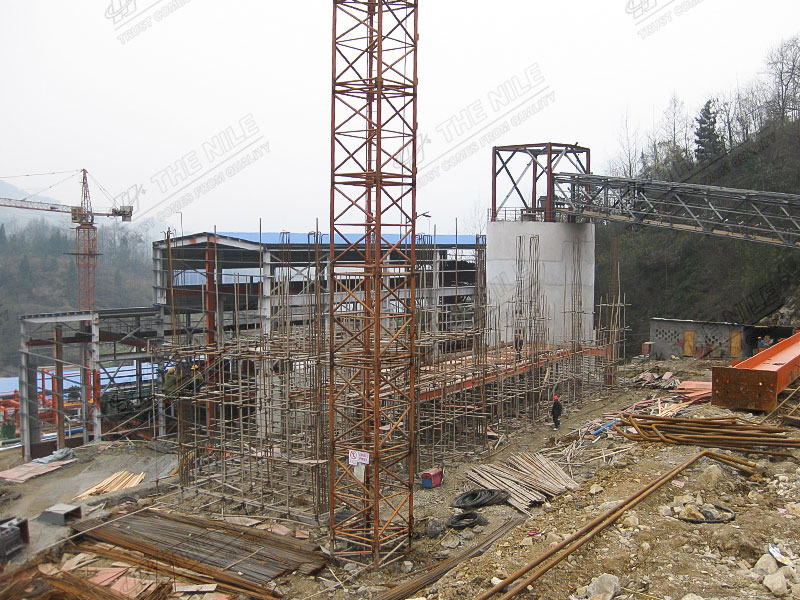
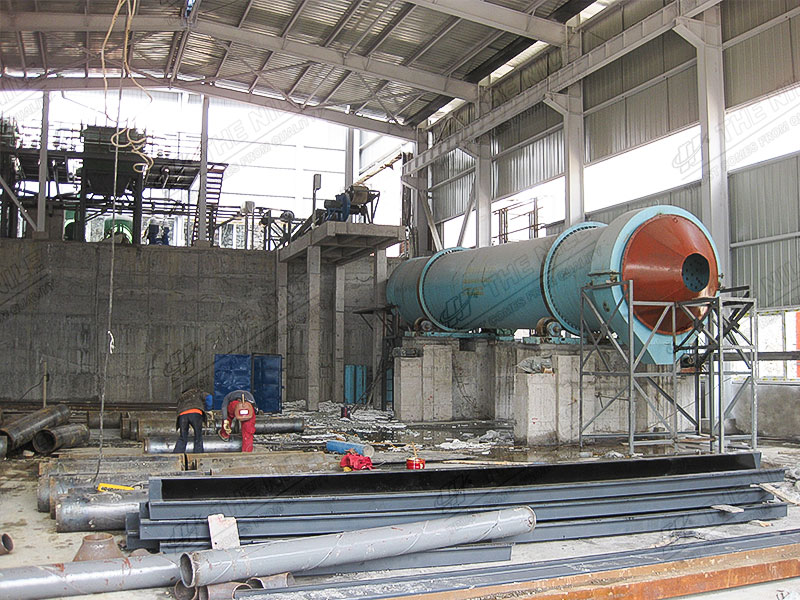
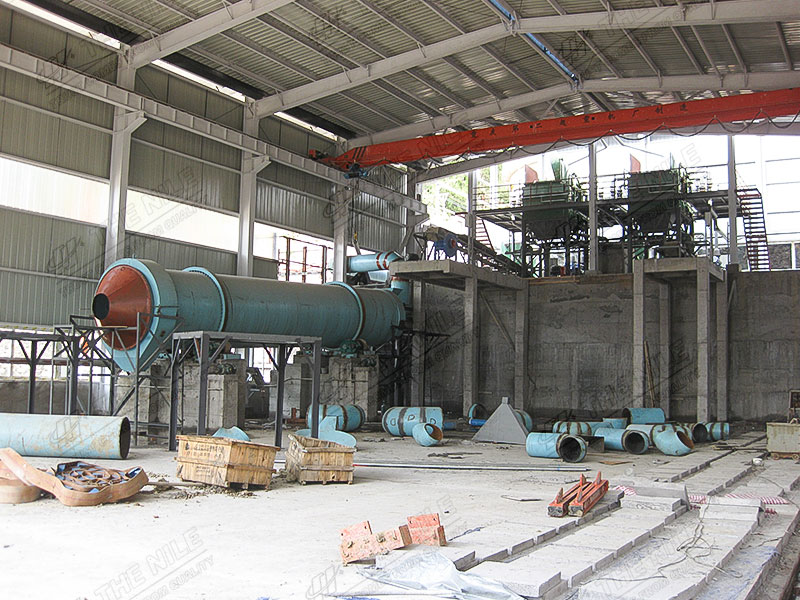
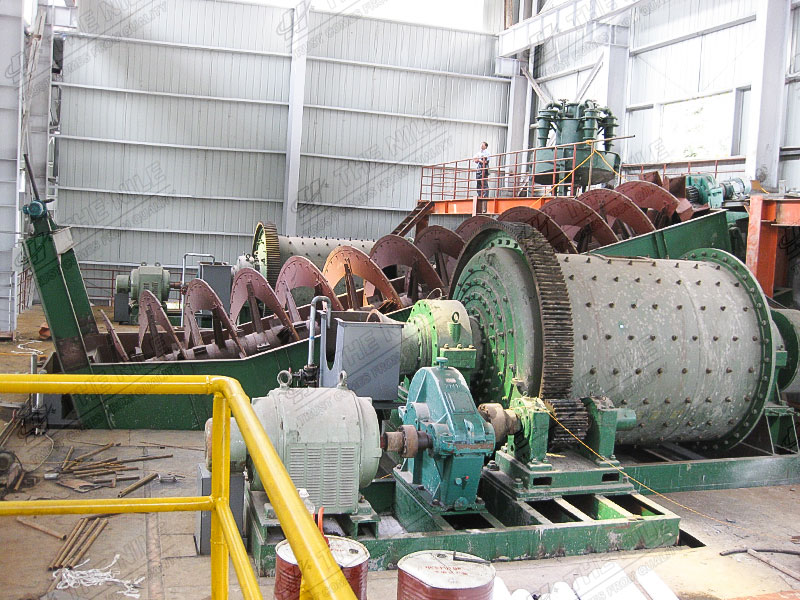
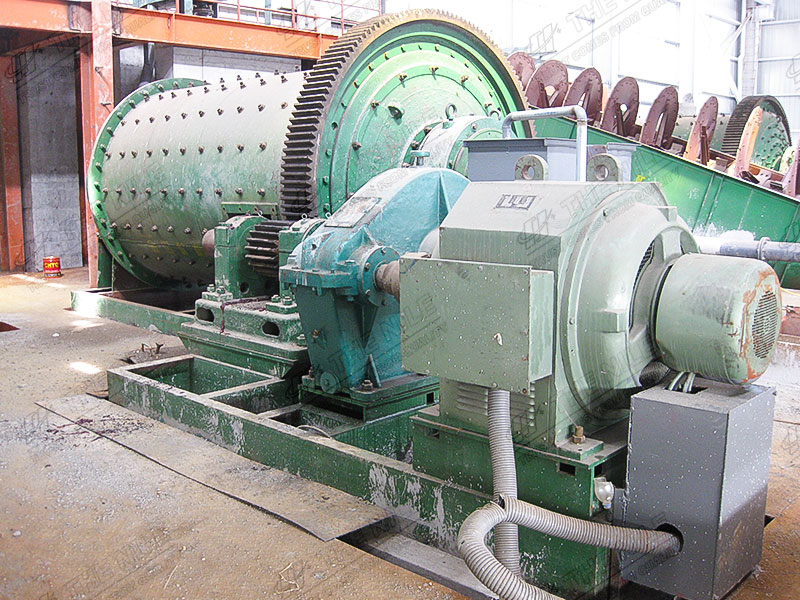
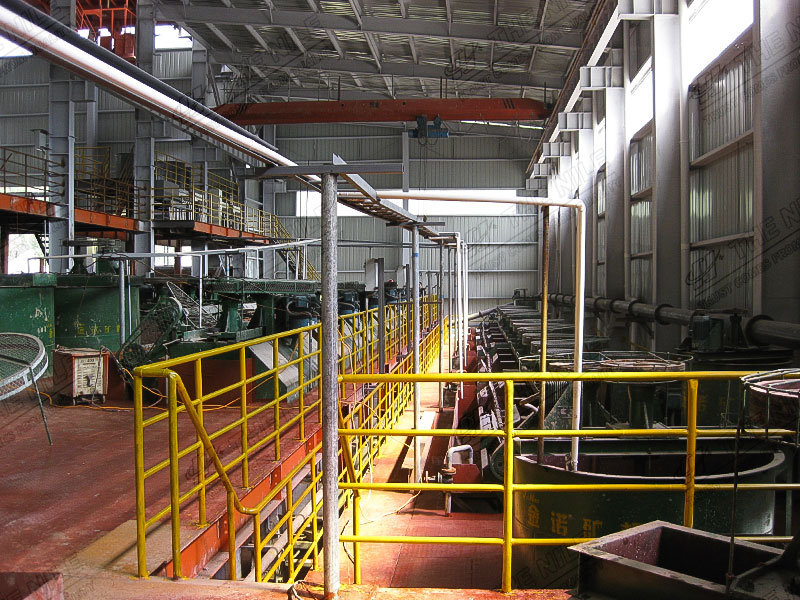
Fluorite ore hand selection method
The hand separation method is mainly used in fluorspar ores where the boundaries between fluorite and gangue are very clear, waste rocks are easy to remove, and various grades of ores are easy to identify with the naked eye. It is the simplest and most economical mineral processing method. The fluorite hand selection method mainly includes washing, screening and hand selection operations. The raw ore after punching and screening can be divided into large pieces, medium pieces, and particles (particle size 6-15mm) and enter the manual selection field. They are manually selected according to grade and stacked by grade. The particle ore enters gravity separation and separation, and is crushed. The chips are processed into fluorspar concentrate through flotation.
Quartz-type fluorite ore:The main minerals are fluorite and quartz, and the fluorite content can reach 80% to 90%. Contains small amounts of calcite, barite and sulfide. Quartz-type fluorite ore is mainly composed of fluorite (content up to about 85%) and quartz, with only a small amount of calcite, barite and sulfide present. The key to sorting is mainly to reduce silicon in the concentrate. To separate quartz from fluorspar, quartz and fluorspar monomers must be dissociated through grinding, so grinding is an important factor affecting quartz-type fluorspar flotation. The most reasonable method is to adopt a staged grinding process, which can not only reduce the silicon content in the fluorspar concentrate after flotation, but also increase the recovery rate of the fluorspar concentrate.
Carbonate fluorite ore: the main minerals are fluorite and calcite. The calcite content can reach more than 30%, with a small amount of quartz, sometimes forming a quartz-calcite-fluorite type ore.
Barite type fluorite ore: the main minerals are barite and fluorite, and the barite content reaches 10% to 40%. This type of ore is often accompanied by sulfides such as pyrite, galena, sphalerite, etc. Sometimes the quartz content increases to form a quartz-barite-fluorite type ore. The flotation of barite-type fluorite ore generally first uses a mixed flotation process and Na2CO3 to adjust the pH value of the slurry, and use oleic acid and water glass as collectors and inhibitors respectively to obtain fluorite and barite. The concentrate is mixed and the barite and fluorite are separated by flotation.
Sulfide-type fluorite ore: Its mineral composition is basically the same as quartz-fluorite, but it contains more metal sulfides, and sometimes the lead and zinc content can reach industrial grades. For sulfide ore-type fluorspar ores, sulfide ore collectors can generally be used to select metal sulfide minerals first, and then fatty acid collectors can be used to recover fluorspar from flotation tailings. In addition, roasting, leaching and other processes can also be used to extract valuable metals and decompose fluorspar. The process flow is relatively simple and can produce high-quality fluorspar products while comprehensively recycling valuable metals.
Application of mineral processing equipment in fluorite ore
Case 1: 500 tons of raw ore are processed daily
Process: 500 tons of raw ore are processed daily. The crushing process is two-stage semi-closed circuit crushing. The crushing particle size is -15mm. The raw ore goes through two stages of closed-circuit grinding. -0.074mm accounts for 78%. The raw ore grade is 21%. After the first coarse, second sweep, and seventh The grade of fluorspar concentrate is 95%, and the recovery rate is 85%. The fluorspar undergoes two stages of dehydration, and the tailings undergo two stages of dehydration and are stacked in dry discharge.
Main equipment: 1 PE600 Jaw Crusher, 1 2YA2148 Vibrating Screen, 1 PEX300*1300 Fine Jaw Crusher, 1 4 1/4 Simons Cone Crusher; 1 MQG2430 Ball Mill, 1 FG- 20Ф2000 Spiral Classifier, 1 MQY2430 Ball Mill, 1 4*250 Cyclone Group, 12 XCF4 Flotation Machines, 22 KYF Flotation Machines; 1 Ф15m Thickener, 1 45㎡ Ceramic Filter, 1 Ф24m Thickener and 1 22㎡ Rubber Belt Filter.
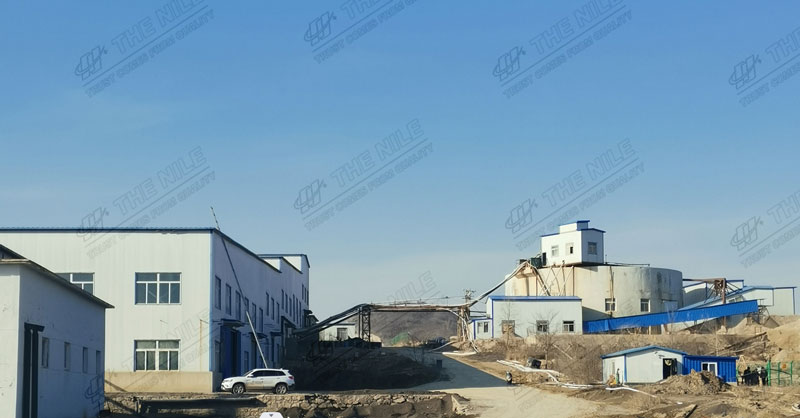
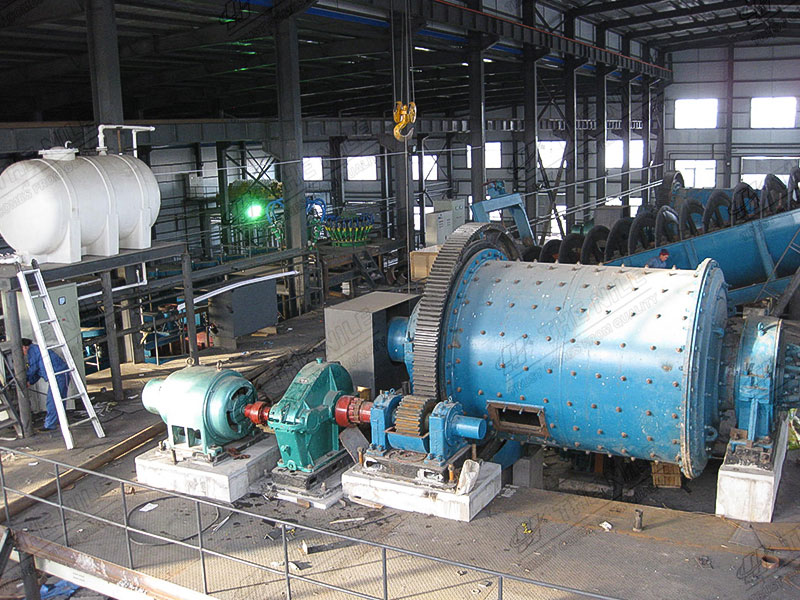
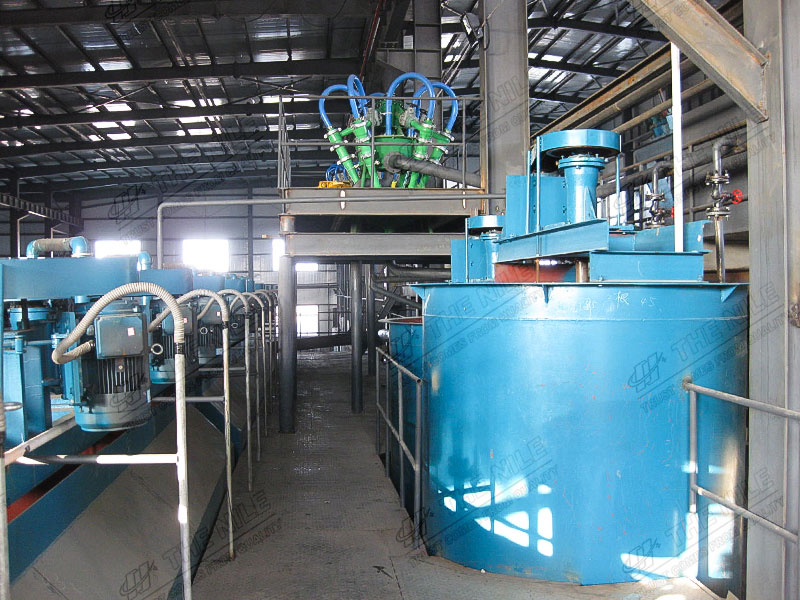
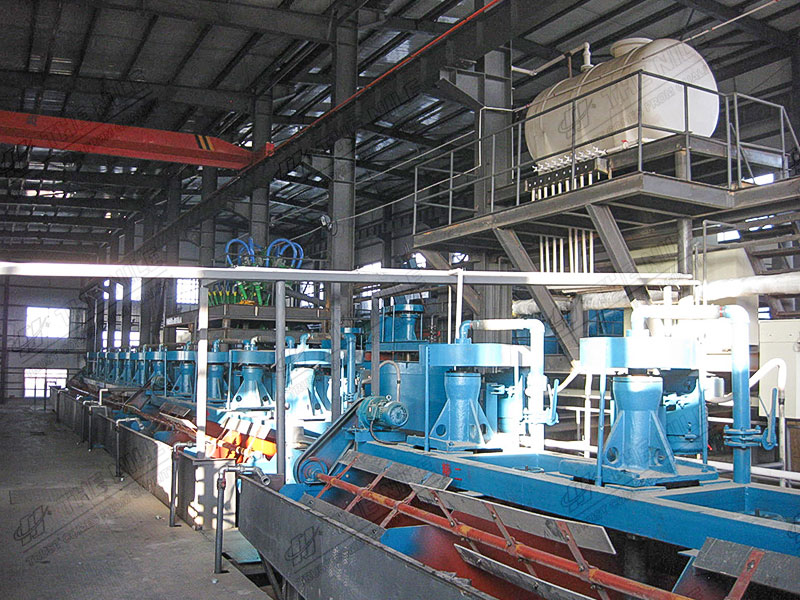
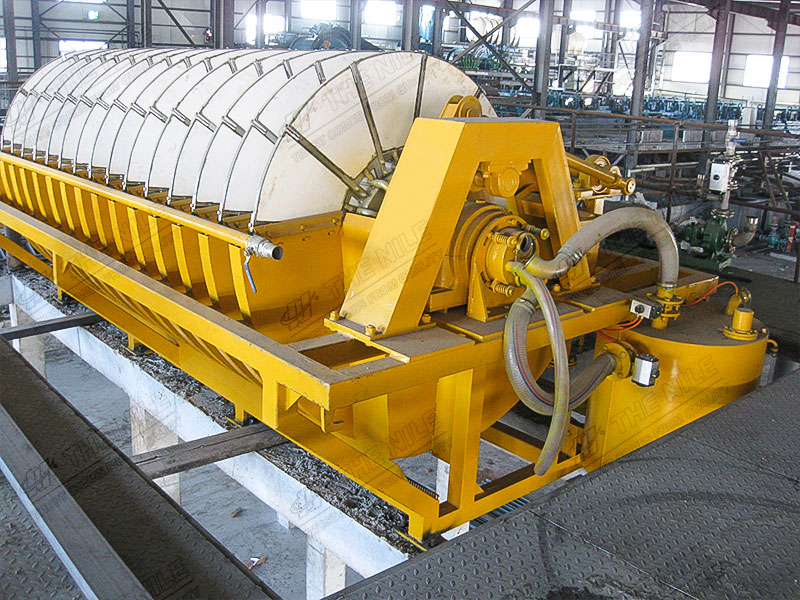
Case 2: 500 tons of raw ore are processed daily
Process: 500 tons of raw ore are processed daily. The crushing process is two stages and one closed circuit. The damage particle size is -15mm. The raw ore is ground in two stages of closed circuit. -0.074mm accounts for 85%. The grade of raw ore fluorite is 40% and barite is 40%. The first Mixed flotation desliming, priority flotation of fluorite, using a semi-open circuit process, fluorite flotation through the first coarse and sixth fine, the concentrate grade is 97%, the recovery rate of fluorite concentrate is 80%; fluorite flotation tailings flotation To select barite, the barite goes through drug-free flotation before flotation, and then goes through primary roughness and secondary fineness. The concentrate grade is 90% and the concentrate recovery rate is 76%.
Main equipment: 1 PE500*750 Jaw Crusher, 1 GP100 Cone Crusher, 1 YA1236 Vibrating Screen, 1 MQG2430 Ball Mill, 1 FG-20Ф2000 Spiral Classifier, 1 MQY2136 Ball Mill, 1 4* 250 Cyclone Groups, 10 BF-8, 25 BF-4, 2 Ф16m Thickeners, 4 20㎡ Disc Type Filters, 2 Ф2*12 Dryers.
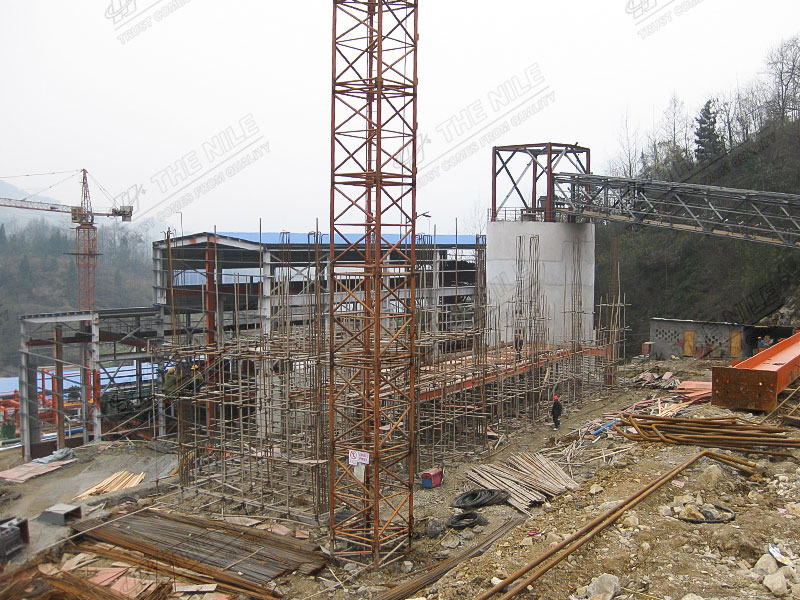
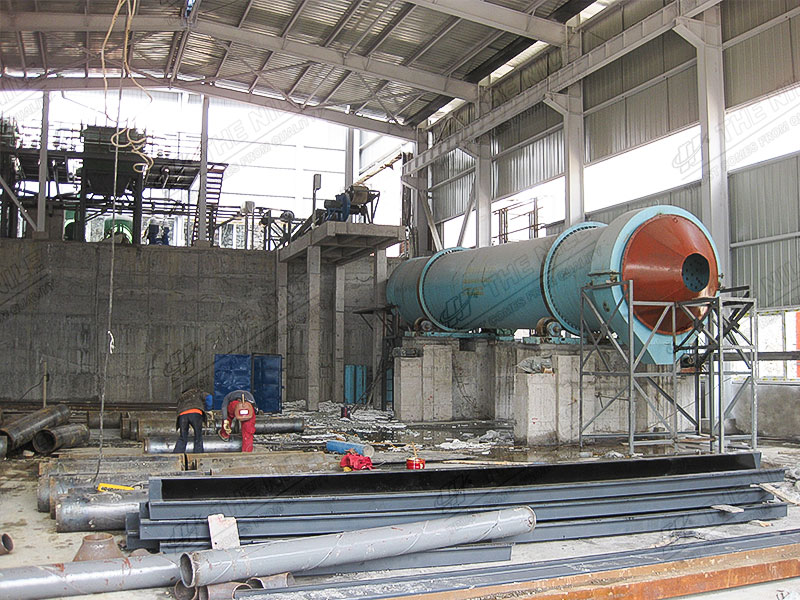
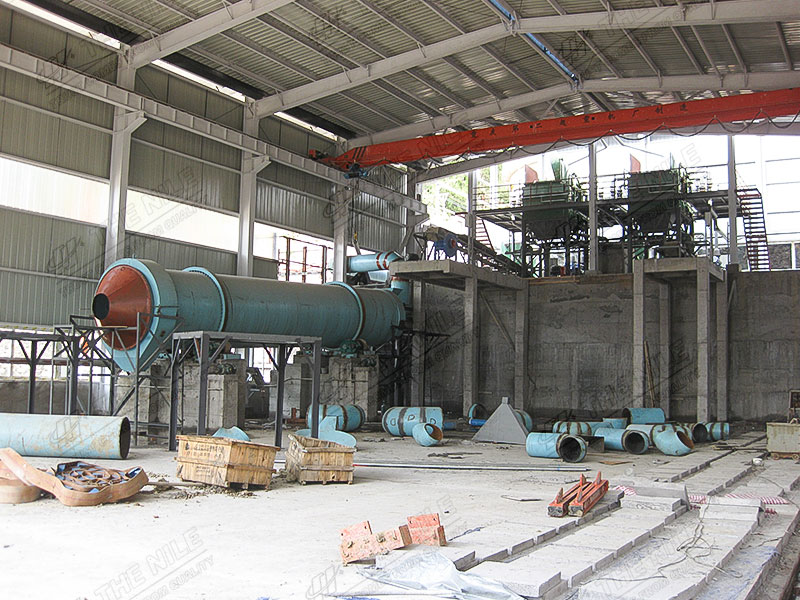
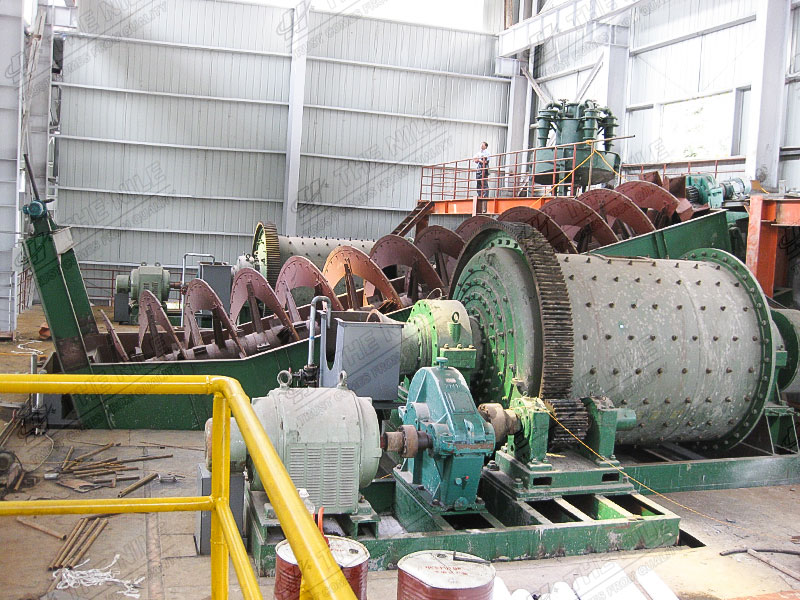
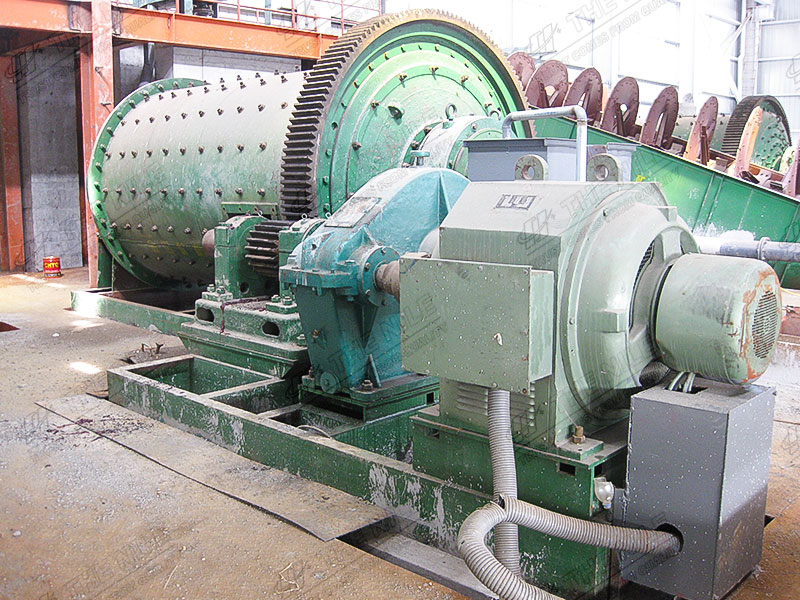
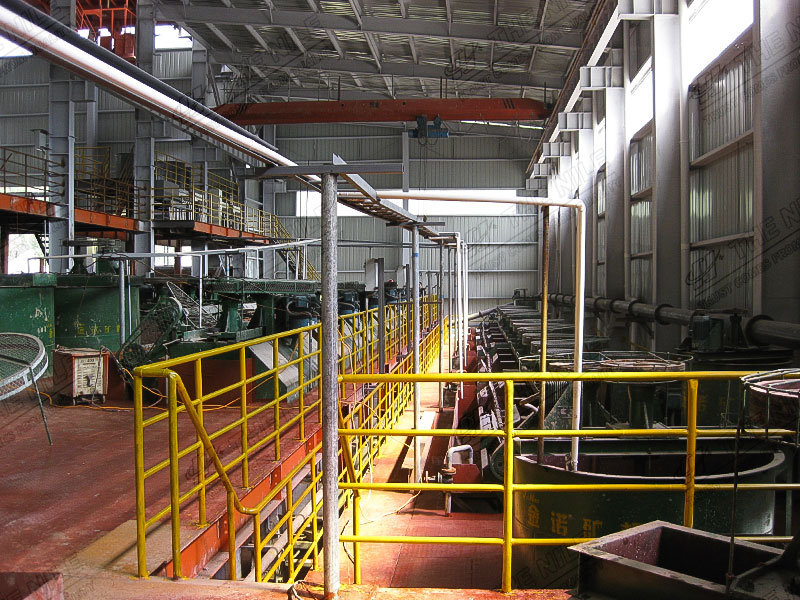
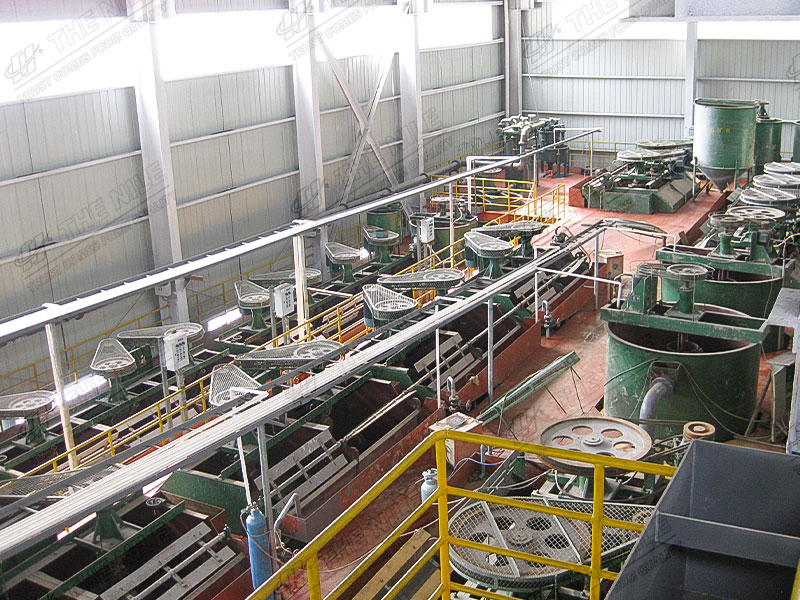
Request for Quotation
You can get the price list and a NILE representative will contact you within one business day.