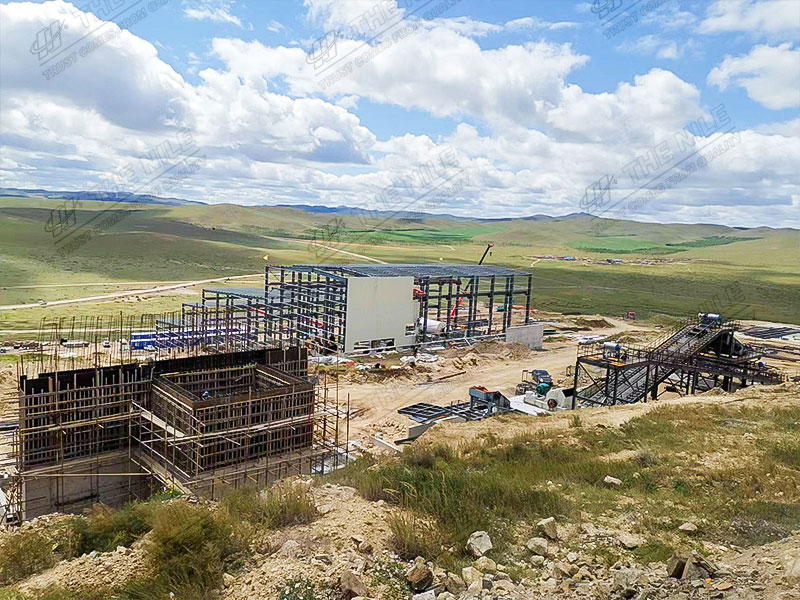
Lead-zinc ore beneficiation process
Easy ways to get the answers you need. Service Online
Lead-zinc ore beneficiation process
·lead-zinc ore:According to the degree of oxidation is divided into sulfide ore and oxide ore; oxidation rate of 10% to 30% of the mixed ore, less than 10% of the sulfide ore, more than 30% of the oxide ore. Lead and zinc ore sorting, mainly flotation, can also use re-election and selection of metallurgical joint process.
·zinc-sulfide ore:
Preferential flotation, mixed flotation, isotropic flotation, split-rate branch flotation, and potentiometric flotation;
·zinc-sulfide ore:
Sodium oxide sulfide flotation method, sulfur sulfide flotation method, flocculation flotation method, and heavy flotation combined separation method;
·mixed lead-zinc ore:
Mixed-Partial Flotation, Mixed-Preferential Flotation.
Lead-zinc sulfide ore beneficiation process
1. Priority flotationThe method is to first suppress zinc and lead floating, and then activate zinc to obtain lead and zinc concentrates (lead and zinc concentrates are recovered in sequence according to the ease of lead and zinc floatability). It is mostly suitable for processing rich ores with simple mineral composition, high lead and zinc grades, and coarse-grained impregnation.
2.Mixed flotation
It is adopted to float the lead-zinc mixed concentrate first, and then separate the mixed concentrate. It is suitable for treating minerals with small differences in lead and zinc floatability, low grade, and useful minerals in aggregates or dense symbiosis.
3.Iso-floatable flotation
Lead-zinc sulfide with similar floatability is divided into two parts of easy-floatable and hard-floatable, and then mixed flotation is carried out separately to obtain mixed concentrate, and then the mixed concentrate is separated. It is mainly suitable for lead-zinc ores containing easy-floatable and hard-to-floatable parts in useful minerals.
4.Fractional speed flotation
Rapid flotation of fast-floating and easy-floating lead-zinc ores respectively. It is mainly suitable for lead-zinc sulfide ores with different flotation behaviors caused by different embedded components.
5.Potential control flotation
It mainly controls the process and direction of the oxidation-reduction reaction on the surface of the sulfide ore in the slurry system by changing the electrochemical conditions of the flotation system, and affects the surface state of the sulfide ore and the product form and stability of the collector on the surface of the sulfide ore. , to increase the hydrophilic-hydrophobic properties of the sulfide ore surface and achieve selective flotation separation.
Oxide Lead Zinc Ore Beneficiation Process
1、Sodium sulfide sulfide flotationThere are two types of flotation: Sulfidation-xanthate flotation and Sulphide-amine flotation, in which:
Sulfidation-xanthate flotation: it is to sulphide the zinc oxide ore (with sodium sulphide) and then flotation, suitable for treating lead oxide ore.
Sulphide-amine flotation: it is the flotation of zinc oxide ore after sulphide, which is mainly suitable for processing zinc oxide ore containing easily muddy veinstones.
2、Sulfur sulfide flotation
Sulfurization of lead-zinc oxide ore using sulfur powder followed by flotation. It is rarely applied at present.
3、Flocculation flotation
It is suitable for the separation of fine-grained lead-zinc ore by adding hydrophobic fine-grained minerals with polymer compounds and vigorously stirring them, and then adding collectors for flotation.
4、Joint selection of re-floating and sorting
The minerals with higher density are first reelected (or reelected pre-tailings) and then separated by flotation. It is suitable for ores with large density difference between useful minerals and vein minerals.
Mixed lead-zinc ore beneficiation process
1、Mixed-partial flotationFirst, the lead-zinc ore in the mixed minerals is recovered, and then the lead and zinc are flotated and recovered through a partial flotation process.
2、Mixing-priority flotation method
Similarly, the mixed minerals are first comprehensively recovered, and then lead and zinc ores are preferentially flotated (based on the preferential flotation of lead sulfide-zinc ores).
The above is a common lead-zinc ore beneficiation process and method, for different regions, different mineral composition, its beneficiation process is different, it is recommended that the first beneficiation test, through the experimental report, customized suitable lead-zinc ore beneficiation process.
Application of mineral processing equipment in lead-zinc ore
Case 1: 1,000 tons of raw ore per dayProcess: 1,000 tons of raw ore per day, crushing process for three sections of a closed-circuit crushing, crushing size -8mm, the raw ore after a closed-circuit grinding, -0.074mm accounted for 70% of the grade of the raw ore lead 1.82%, zinc grade 1.53%, the priority of flotation lead, lead tailings and then flotation of zinc, lead and zinc flotation is a roughing, three sweeps, four selections, lead concentrate grade 60%, lead concentrate The lead concentrate grade is 60% with a lead concentrate recovery rate of 83% and the zinc concentrate grade is 51% with a zinc concentrate recovery rate of 79%. The tailings are dewatered in three stages: dewatering screen, thickener concentration and filter press, and the tailings are transported to the tailings warehouse for dry-discharge stockpiling.
Main equipment: 1 PE600 jaw crusher, 1 PYB1200 cone crusher, 1 2YA3075 circular vibrating screen, 1 set of 2000 hammer crusher, 1 set of MQG2760 ball mill, 1 set of 4*350 cyclone group, 10 sets of XCF10 flotation machines, 14 sets of KYF10 flotation machines, 8 sets of XCF4 flotation machines, and 2 sets of KYF4 flotation machines; There are 2 Ф9m thickeners, 2 Ф28m thickeners, 2 6㎡ disc filters, 1 2142 dewatering screen, 1 8*250 cyclone group, and 3 500㎡ plate and frame filter presses.
![]() |
![]() |
![]() |
![]() |
![]() |
![]() |
![]() |
![]() |
Case 2: The raw ore processing capacity is 300t/d
process:The raw ore processing capacity is 300t/d. The crushing process is two stages and one closed-circuit crushing. The crushing particle size is -20mm. The raw ore grade is lead 1.24 and zinc 5.15. The raw ore goes through one stage of closed-circuit grinding. -0.074mm accounts for 68%. Priority is given to lead flotation and lead selection. The tailings are re-flotated for zinc, and the lead-zinc flotation involves one roughing, three scavenging, and four selections. The lead concentrate grade is 56%, the lead concentrate recovery rate is 93%, the zinc concentrate grade is 50%, and the zinc concentrate The ore recovery rate is 82%. After two stages of dehydration, the tailings are discharged to the tailings pond.
Main equipment: 1 PE600*900 jaw crusher, 1 PYZ1200 cone crusher, 1 MQG2145 ball mill, 1 FG-15Ф1500 spiral classifier, 1 SF4 flotation machine, 30 SF4 flotation machines, 2 Ф6m
![]() |
![]() |
![]() |
![]() |
![]() |
![]() |
Request for Quotation
You can get the price list and a NILE representative will contact you within one business day.